Paperless Parts CPQ is a cloud-based solution machine shops in industries like aerospace, defense, industrial, and medical devices use to deliver quotes and cost estimates when selling highly configurable products. With its AI-powered quote setup and automated data extraction from RFQ emails, Paperless Parts eliminates repetitive, error-prone tasks. It offers a centralized repository that enhances visibility into quote status and historical data. The system leverages advanced geometric analysis to improve the speed and accuracy of quotes. These features make it an ideal choice for manufacturers looking to streamline their quoting process and reduce the risk of costly mistakes when configuring complex products.
Manufacturing companies benefit from Paperless Parts CPQ by transforming their sales and quoting workflows. The platform’s unique features, such as 2D and 3D CAD file viewing, geometric feature analysis, and advanced analytics, allow teams to quickly identify manufacturability issues and optimize pricing strategies. These capabilities, combined with secure in-app collaboration and customizable workflows, make Paperless Parts a standout solution in the manufacturing industry.
Why this product is good
Positives of Paperless Parts Software
Product Details
What is Paperless Parts?
Paperless Parts is a comprehensive, feature-rich quoting software for manufacturing companies. It helps manufacturers deliver professional, easy-to-understand quotes to buyers who need highly configurable products like heavy machinery or complex aerospace components.
For manufacturers, its most valuable features include:
- Advanced geometric analysis
- Robust configuration logic
- 2D and 3D CAD file viewing
- Holistic RFQ management
- In-app collaboration features
- AI-powered automation
- Dynamic lead times and pricing options
- PDF comparison and redaction
Advanced geometric analysis: Paperless Parts CPQ leverages a powerful geometry engine that analyzes parts based on various manufacturing processes (e.g., CNC machining, rubber manufacturing, additive manufacturing). The engine identifies potential issues, such as tight corners or deep holes, which require special tooling and incorporates them into the final estimate. You can tailor the thresholds for manufacturability detection to fit your shop’s capabilities. This detailed analysis level ensures manufacturers can catch manufacturability issues early, reducing errors and costs associated with rework.
Robust configuration logic: The Paperless Parts Pricing Language (P3L) makes it easy for you to configure the system to match your unique pricing models and workflows. This flexibility ensures that every manufacturer, regardless of their specific needs, can tailor the system to fit their exact requirements. This adaptability is complemented by robust customer support and enablement teams that help set up and fine-tune the system, ensuring it aligns perfectly with the company’s strategic goals
2D and 3D CAD file viewing: The platform supports 2D and 3D CAD file viewing, enabling detailed annotations and discussions directly within the software. It also integrates seamlessly with other essential systems like ERP, enhancing data flow and reducing the need for multiple software solutions. This integrated approach streamlines the entire quoting process, from RFQ to final quote, ensuring that all relevant information is centralized and easily accessible.
Holistic RFQ management: The platform provides a centralized dashboard to manage RFQs, significantly streamlining the process of collecting, sorting, and prioritizing requests. The ITAR-compliant Smart RFQ Form, which you can embed directly onto website, enhances this centralized approach, eliminates the need for manual data entry, and speeds up response times. This capability ensures that all RFQs are handled efficiently and effectively, reducing the risk of missed opportunities and errors.
In-app collaboration features: Users can highlight features or measurements on 3D models or prints directly within the platform, ensuring clear communication and reducing the risk of miscommunication. Additionally, the platform provides real-time visibility into the status of every quote, helping teams identify and address bottlenecks promptly. This comprehensive visibility and collaborative environment enhance overall workflow efficiency and accuracy.
AI-powered automation: The system utilizes AI to automate critical aspects of the quoting process, such as the setup of new quotes from RFQ emails. This automation not only speeds up the process but also reduces human error by automatically attaching and organizing all relevant files. The AI-supported Part Setup tool identifies and suggests critical part data, further minimizing time spent on manual tasks and enhancing accuracy.
Dynamic lead times and pricing options: Paperless Parts allows manufacturers to offer multiple lead time and price combinations on their quotes. This feature helps shops increase their margins, improve win rates, and speed up order intake by aligning more closely with where buyers see value. By providing expedite options, manufacturers can cater to urgent customer needs while capturing higher margins, ultimately enhancing the overall customer experience.
PDF comparison and redaction: The platform includes advanced tools for comparing and redacting PDFs, which are particularly valuable for handling drawing revisions and maintaining data security. Users can overlay PDFs to quickly identify changes, saving significant time and reducing the likelihood of errors. The PDF redaction tool allows users to easily and securely redact sensitive information directly within the platform, eliminating the need for external software and ensuring data integrity.
What are the advantages of using Paperless Parts?
Paperless Parts Benefits
For manufacturers, there are several advantages to using Paperless Parts for quoting and cost estimation. The most notable ones include:
- Increased sales efficiency and productivity by automating manual tasks and streamlining the quoting process
- Enhanced quote accuracy with its advanced geometric analysis, configuration logic, and AI-supported automation
- Better resource utilization and cost reduction through optimized workflows and RFQ management
- Improved customer experience with faster response times, dynamic lead times, and visual collaboration features
- Data security and compliance with ITAR-compliant forms, US-based system administrators, FedRAMP Moderate Equivalent CMMC compliance, and cloud-native software hosted on GovCloud
- Flexibility and adaptability with the ability to configure the system to fit unique pricing models and workflows
- Centralized data and information through 2D and 3D CAD file viewing, ERP integration, and a centralized dashboard for RFQ management
- Comprehensive onboarding and enablement from dedicated teams to ensure manufacturers can maximize the benefits of the platform
What industries are best suited for this solution?
Paperless Parts for Industries
Within manufacturing, several different industries can benefit from using Paperless Parts. Some of these include:
Aerospace and Defense
Efficient handling of large and complex parts/assemblies: The platform allows users to quickly build and reconfigure bills of materials (BOMs) for 500+ part assemblies. This feature allows manufacturers to quickly extract tree structures from CAD files, modify and arrange product assemblies, and transform subassemblies into purchased components. This gives BOMs and routing steps a smooth transfer from Paperless Parts to their ERP systems.
Enhanced security and compliance: Paperless Parts is ITAR-registered and offers a FedRAMP Moderate Equivalent solution, ensuring compliance with CMMC and other regulatory standards. This allows manufacturers to protect their customers’ intellectual property securely, share files selectively, prevent unauthorized downloads, and set expiration dates for data access. This high level of security is crucial for handling Controlled Unclassified Information (CUI) and passing CMMC audits, making Paperless Parts a reliable choice for defense contractors.
Rapid quoting with detailed analysis: The platform uses advanced geometric analysis to provide detailed insights into part manufacturability, including dimensions, tolerances, parallelisms, datums, and text annotations directly from Model-Based Definition (MBD) files. This capability is particularly valuable for aerospace and defense manufacturers who often work with parts that have uniquely tight tolerances and require adherence to specific military and ASTM standards.
Heavy Machinery
Advanced costing engine: Heavy machinery components tend to be bulky and unwieldy, necessitating specialized handling and considerable setup time. Paperless Parts’ costing engine gives manufacturers the power to automatically pinpoint part characteristics that influence production time and expenses, including the requirement for forklifts and additional labor to transport parts around the workshop.
Increased flexibility in lead times: The demand for heavy equipment parts can fluctuate significantly, and meeting production volume requirements within tight timelines is a common challenge. And fast turnaround times are often prioritized over pure unit cost. Paperless Parts enables manufacturers to offer dynamic lead times with adjusted pricing, allowing them to capture increased margins by providing flexibility to their customers.
Efficient management of complex BOMs: Users can reconfigure BOMs to match their specific manufacturing processes, convert subassemblies to purchased components, and handle extensive part assemblies with ease. This reduces the administrative burden and potential errors associated with manual data entry, streamlining the entire quoting process from start to finish.
Medical Devices
Quality control and regulatory compliance: Paperless Parts ensures that all configurations comply with stringent industry regulations, such as ISO 13485, ISO 14971, and FDA 21 CFR Part 11. The platform supports digital documentation storage, revision control, and real-time collaboration, ensuring that all relevant documents are easily accessible and up to date. This helps manufacturers maintain high quality and traceability, reducing the risk of non-compliance and product recalls.
Customized routing and quote templates: The platform allows medical device manufacturers to create customized routing templates that include quality assurance specifications such as first article inspections, custom sampling plans, and production part approval process (PPAP) specs. This ensures that all critical quality checks and controls are accurately costed and included in the quoting process, regardless of who is generating the quote.
Advanced analytics for better decision-making: Paperless Parts provides advanced analytics that enable manufacturers to analyze multiple layers of data to optimize front office operations, prioritize quotes, and price work effectively. By understanding win rates by customer, geometry, or material, medical device manufacturers can make impactful business decisions, improve operational efficiency, and identify their most profitable jobs.
Prices
Paperless Parts Pricing
Given the complex and customizable nature of the platform, Paperless Parts CPQ’s pricing is based on each manufacturer’s specific needs and requirements. Contact Paperless Parts directly via their website to request a demo and receive a personalized quote for your business.
Is there anyone else out there?
Competitors and Alternatives to Paperless Parts
Manufacturers are the primary users of Paperless Parts. Below are several Paperless Parts alternatives that also cater to this industry.
Top Paperless Parts Alternatives
Cincom CPQ
Cincom CPQ offers a powerful suite of features designed for contract manufacturers and complex engineer-to-order sales processes. With advanced 3D modeling and visualization, a built-in ROI calculator, and an intelligent configuration rules engine, Cincom CPQ enhances the sales experience by enabling personalized, accurate, and efficient quoting. Its seamless integration with enterprise systems like CRM, ERP, and B2B eCommerce ensures smooth workflows, while native tools for customer communications and custom application development provide added flexibility. As a cloud-based, customizable platform, Cincom CPQ empowers manufacturers to streamline operations, improve accuracy, and drive business growth.
Configit CPQ
Configit CPQ empowers manufacturing sales teams to sell complex products and generate accurate quotes efficiently. Its proprietary Virtual Tabulation® technology ensures 100% valid configurations, reducing errors and streamlining sales processes. Configit provides advanced 3D visualization, enabling sellers to present interactive product models to customers. With declarative modeling, users can define configuration rules to maintain manufacturability and accuracy, while the Solution Space feature helps optimize product combinations for sales and production planning. Seamless integrations with SAP, Salesforce, and Microsoft Dynamics further enhance operational efficiency, making Configit an ideal choice for industries like industrial automation, medical devices, and renewable energy.
Infor CPQ
Infor CPQ is an industry veteran that’s been around for more than two decades. It offers manufacturers a quoting and ordering system with customization and visualizations (including augmented reality), automated manufacturing instructions, and extensible developer tools. Where it sets itself apart is with its system integrations. Through Infor’s sophisticated Platform-as-a-Service (PaaS) solution and its API gateway, users can integrate enterprise systems — on-premise, hybrid, or cloud-based. It also integrates with Infor Birst®, the vendor’s world-class business intelligence platform. Consider Infor CPQ if your organization needs immersive AR experiences, enterprise-level customizations and integrations, or integrated BI tools.
XaitCPQ
XaitCPQ is a highly intuitive CPQ tool with 70,000+ customers ranging from SMB manufacturers to Fortune 500 enterprises. While Paperless Parts primarily targets American companies (and excels at it), XaitCPQ offers international security (ISO/IEC 27001) and data privacy (GDPR) that make it suitable for multinational corporations. For manufacturers, XaitCPQ also has a guided selling feature that helps your sales team quickly and easily configure complex products. Consider XaitCPQ if you’re a manufacturer that needs international support from your CPQ solution.
Configure One CPQ
Configure One CPQ simplifies complex product configurations, generates dynamic quotes with visuals and BOMs, and leverages real-time production data—all within a single platform. Beyond quoting, it includes specification sheet configuration, order invoicing, and historical document tracking for easy reference. Configure One enhances accuracy with guided selling and constraint management and fosters real-time collaboration between sales, engineering, and production. Its integrated CAD automation eliminates manual updates, while seamless integrations and customization options ensure a flexible, scalable CPQ experience.
FAQs
Common Questions and Answers
Paperless Parts improves manufacturing job estimating by streamlining the quoting process, reducing administrative burden and potential errors associated with manual data entry. Its CPQ features enable customized routing and quote templates with quality assurance and advanced analytics, resulting in more accurate quotes and enhanced operational efficiency.
The Paperless Parts platform is API-based, meaning it enables seamless integration with all the essential systems in your tech stack. This includes your ERP system, CRM software, accounting tools, and many others.
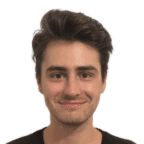
Andrew is a professional copywriter with expertise in creating content focused on business-to-business (B2B) software. He conducts research and produces articles that provide valuable insights and information to his readers.